Comment est conçu le Halo qui protège les pilotes ?
La conception et la construction du Halo reposent sur des principes et des matières permettant d'augmenter drastiquement la sécurité des pilotes.
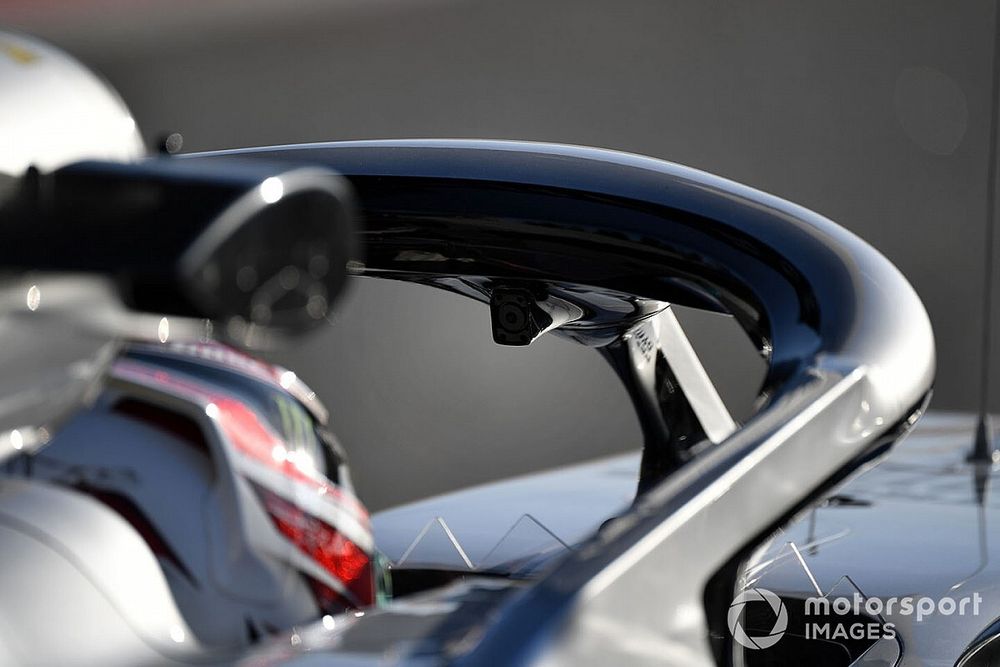
Photo de: Mark Sutton / Motorsport Images
Très critiqué lors de sa présentation puis de son introduction pour des questions d'ordre esthétique, le Halo est devenu obligatoire sur les monoplaces des championnats FIA, avant de prouver son efficacité à plusieurs reprises. Sa conception et sa création vont toutefois bien plus loin que l'aspect esthétique, puisque la FIA explique qu'il est fait pour résister au poids de deux éléphants d'Afrique, tandis qu'il est aussi assez robuste pour encaisser le choc d'une valise lancée à 225 km/h.
Le Halo est fabriqué en titane de Grade 5, qui est plus précisément un alliage fait de 6% d'aluminium, de 4% de vanadium, de 0,25% de fer et de 0,2% d'oxygène, tandis que le reste de la composition est du titane pur. Tout en gardant la même rigidité que du titane pur, cet alliage est plus solide et peut être traité pour résister à la chaleur. C'est un matériau utilisé notamment dans l'aviation et dans l'industrie aérospatiale qui, en plus de ses propriétés de résistance, affiche un poids limité sur la balance.
CP Autosport est un des trois fournisseurs désignés par la FIA pour le Halo, et ce fut la première entreprise à passer les tests et à être choisie par neuf des dix équipes. Certains teams ont décidé de s'approvisionner auprès des trois fournisseurs, mais CP Autosport a été le plus plébiscité et a ainsi dû passer commande rapidement d'une quantité non négligeable de matières premières, comme l'explique un des responsables du projet, Steffen Zacharias.
"Nous avons dû acheter environ dix tonnes de titane à haute résistance en un mois et demi, et nous avons tout reçu à temps, avec une qualité parfaite", révélait-il avant l'introduction du système en F1. "Nous avons une longue histoire en sport automobile, nous y sommes impliqués depuis les années 90, et nous avons un historique encore plus complet en matériaux aérospatiaux ainsi que dans leur fabrication. Il faut des machines de haut niveau pour la manufacture avant et après le soudage."
Le processus commence par le traitement de résistance à la chaleur, généralement effectué sur les blocs de titane avant que CP Autosport ne les reçoive, avec une spécification toutefois demandée par l'entreprise allemande. La deuxième étape est la manufacture des tubes qui sont ensuite soudés ensemble, puisque le Halo lui-même est constitué de cinq pièces. La partie supérieure, la plus épaisse du système, est constituée de deux pièces en forme de quart de cercle assemblées, auxquelles sont ajoutés les deux supports arrière et le pilier central.
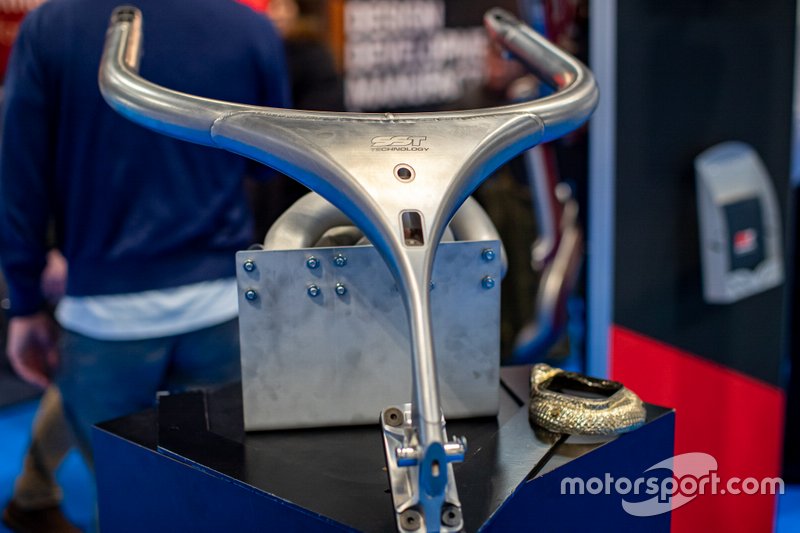
Le protocole de soudure est effectué en pièce close pour éviter que tout objet, même d'une taille minime, ne vienne fragiliser l'ensemble. Une fois assemblé dans sa forme définitive, le Halo subit un nouveau traitement pour la chaleur et on lui ajoute des renforts. C'est après cette étape qu'ont été effectués les tests de résistance pour s'assurer que le système était en accord avec les normes de crash-test voulues par la FIA, ce qui a permis son approbation par l'institut de sécurité affilié à la fédération.
Outre les tests de sécurité, chaque Halo produit par CP Autosport est également vérifié dans sa constitution et dans son assemblage. Sa géométrie est vérifiée, tout comme son poids, et il est passé aux rayons X pour détecter d'éventuelles fissures : "Nous faisons ces tests dans nos infrastructures", poursuit Zacharias. "Grâce à notre expérience dans l'industrie aérospatiale, nous avons une zone de tests importante, avec des bancs d'essais physiques et des processus de tests pour le cycle de vie [des objets]. Nous faisons vérifier nos pièces par des personnes certifiées aux standards de l'aérospatiale."
Un processus complexe et complet qui permet d'assurer la sécurité des pilotes puisque le système est conçu pour résister à 125 kiloNewtons de force verticale, ce qui équivaut à un poids de 12 tonnes, pendant cinq secondes sans rupture de la part de la cellule de survie, des montants ou des attaches. Le Halo est capable de résister à la même force latéralement, ce qui en fait l'élément le plus solide sur une monoplace actuelle.
Selon Zacharias, tout cela a été possible grâce à un travail en toute transparence avec les équipes : "C'était une tâche difficile de réunir ces technologies de production sur une telle pièce. Je suis dans le milieu depuis près de 20 ans et je n'avais jamais vu une telle porte ouverte de la part des équipes. Quelle que soit la question que nous nous posions, quel que soit l'expert auquel nous devions parler, nous avons été mis en relation. Toutes les portes ont été ouvertes."
CP Autosport, qui produit habituellement des pièces invisibles de l'extérieur d'une monoplace, est heureux d'afficher un de ses produits aux spectateurs de la F1, mais aussi des catégories inférieures et de la Formule E : "Nous avons 200 personnes qui travaillent ici et nous produisons habituellement des parties qui sont sous la voiture et couvertes par la fibre de carbone. Pouvoir montrer une pièce physique qui est visible pour le public permet à nos employés de dire 'c'est ce sur quoi je travaille'. Ça nous rend fiers."
Be part of Motorsport community
Join the conversationShare Or Save This Story
Subscribe and access Motorsport.com with your ad-blocker.
From Formula 1 to MotoGP we report straight from the paddock because we love our sport, just like you. In order to keep delivering our expert journalism, our website uses advertising. Still, we want to give you the opportunity to enjoy an ad-free and tracker-free website and to continue using your adblocker.
Top Comments